Powering Off-Site Construction with Robotics for Unmatched Precision and Efficiency
Off-site and volumetric building construction is only as effective as the technology powering it. Automation solutions provider Adelphi Automation offers companies in the world of Modern Methods of Construction the technology to make projects truly modern.
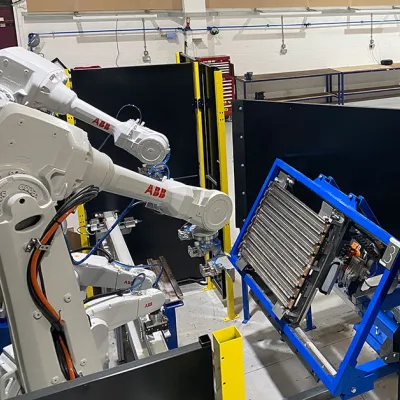
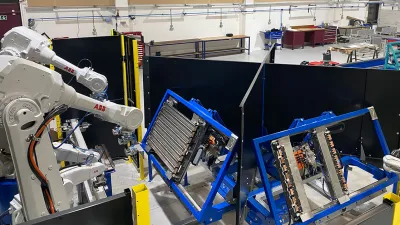
Despite the many significant advances made in modernising the construction industry, it remains awe-inspiring to see robotics at work building our homes, schools, and hospitals. From autonomous vehicles to robotic welders and 3D concrete printers, the potential for robots building alongside skilled human workers is tremendous. Indeed, the global construction robotics market is expected to reach US$774.6 million by 2032.
As more construction projects turn to off-site manufacturing and modular assembly as the preferred method of building, we may see fewer robots on live construction sites, but instead in controlled and scalable factory settings. This will make the need for greater automation in these manufacturing facilities more pronounced.
Adelphi Automation is an automation solutions business with two decade’s worth of experience automating off-site building and assembly processes for the construction sector. It has a team of more than 20 engineers and systems-support staff based in a 14,000 square foot facility in Co. Westmeath. Adelphi Automation is pivotal in the design, delivery, commissioning, and support of innovative projects for clients which ensure bottom line profitability and help them stay ahead of production requirements.
The company’s bespoke automation projects range from adding automatic lines building lintels and wall brackets to existing manufacturing infrastructure up to factory wide automation. This also includes advanced consultancy on a manufacturing centre's supply chain, facility outputs, and relevant modern methods of construction.
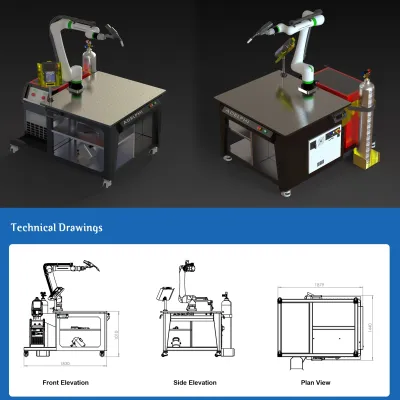
By automating production operations, and building up the output of prefabricated assemblies and whole modular units, off-site construction can lead to quicker installation and shorter project timelines. The greater production precision gained through automation can also reduce the risk of damage or faults in manufacturing.
A recent project with IJM Timber Framing, an off-site manufacturer with expertise in designing and installing timber and steel frame buildings, showcases the potential of robotics in off-site manufacturing. IJM required support in integrating robotic welding into steel frame production, to increase the output of prefabricated residential houses.
IJM has two experienced steel welders on-staff but wanted to supplement this with a robotic welding cell capable of 1.5x the output of a new hire. The robot would work alongside the welders while they performed regular quality checks on its work. The welders can now complete more work while also undertaking quality control and assurance, reducing their physical workload and enriching their vocation.
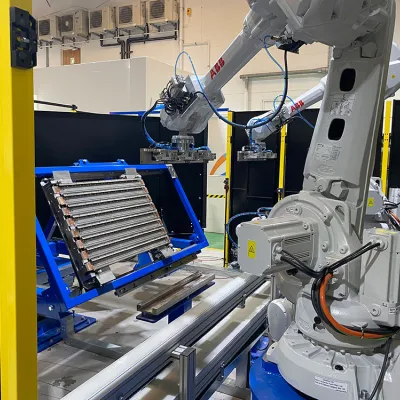
Gary Monks, Business Development Manager for Adelphi Automation, explained how the installation and deployment of this robotics infrastructure worked.
Our first step was to assess IJM’s manufacturing facility for the technical specifications of the welding cell they would need. Then we needed to programme our robotic units to the precise manufacturing specifications of the company’s needs, including the technical details of the steel being welded.
Business Development Manager for Adelphi Automation
This process is individualised to each company, with Adelphi Automation’s robotics solutions highly adaptable to different projects.
The pre-programming we do allows our cells to react to the conditions of the metal being welded. This ensures a high level of quality and safety compliance is maintained without the need to quality check the process regularly.
Business Development Manager for Adelphi Automation
Robotics integration into IJM’s steel frame production, when calculating return on investment, means this sophisticated system pays for itself within just three years.
Robotics is transforming construction by ensuring high quality, durable, and scalable outputs because the process is carried out the same way every time. Rather than replacing workers, people will work alongside automated systems, blending onsite, practical site knowledge with digital expertise. This shift is creating demand for roles like robotics technicians and automation specialists. To stay competitive, the industry must invest in upskilling and re-skilling to build a workforce ready to manage, maintain, and collaborate with robotic systems onsite.
Additive manufacturing is critical for moving projects from live building sites to controlled, endurable, and saleable construction assembly facilities. Robotics may just be one piece of this puzzle, but it certainly looks to capture the most striking headlines.