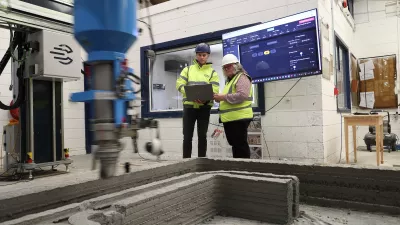
What is MMC?
Modern Methods of Construction (MMC) are a range of innovative building techniques that aim to improve efficiency, productivity, sustainability, and quality in the construction industry. By shifting much of the construction process away from traditional onsite methods and towards factory-based or digitally enabled approaches, MMC transforms how we design, construct, and deliver buildings.
MMC includes practices such as:
- Offsite Construction – manufacturing components like walls, floors, or even entire modules in controlled factory environments.
- Digital Design and BIM (Building Information Modelling) – using digital tools to improve accuracy, collaboration, and project outcomes.
- Advanced Materials and Techniques – applying new materials and processes that enhance building performance and reduce environmental impact.
- Lean Construction – optimising workflows to minimise waste and increase value throughout the project lifecycle.
At its core, MMC is about building smarter – enabling faster delivery, better quality, and reduced carbon emissions.
The Seven Categories of MMC
Modern Methods of Construction (MMC) is a term to describe a range of manufacturing and innovative alternatives to traditional construction. MMC can help boost productivity and efficiency of construction projects.
There are seven categories of MMC (as defined by the UK’s MMC framework) which reflect the diverse range of innovative approaches in construction, from pre-manufacturing to on-site techniques.
Check out below introductory videos (commissioned by the Department of Further and Higher Education, Research, Innovation and Science) as Harrison Gardner provides an overview of each of the MMC categories.
Harrison Gardner introduces MMC
The Department of Further and Higher Education, Research, Innovation and Science has created eight videos, in conjunction with industry leaders and TV personality Harrison Gardener, to give Irish construction businesses a solid grounding in the fundamentals of Modern Methods of Construction (MMC).
This series will also illustrate how advanced technologies and digital processes will transform Irish construction in a simple and accessible way.
The first of these videos introduces you to Modern Methods of Construction.
Check out this introductory video and the following videos with Harrison Gardner, as he provides an overview of each of the categories.
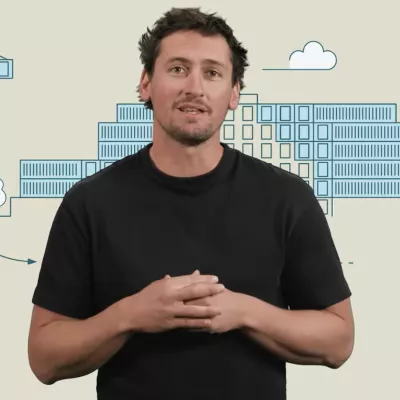
1) Pre-Manufacturing: 3D Systems
This involves constructing three-dimensional units in a factory setting, which are then transported to the site for assembly. These modules can be fully finished, with internal fittings and services installed, before they even reach the site for efficiency and to reduce the time spent onsite.
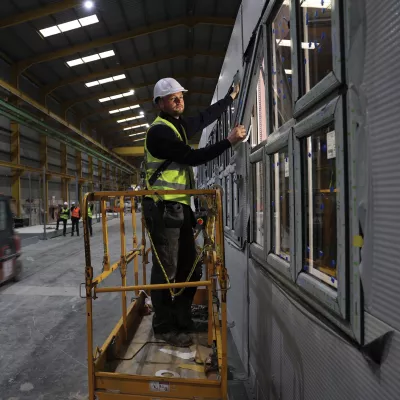
2) Pre-Manufacturing: 2D Systems
These are flat panels that are manufactured off-site and assembled onsite to form a building. They can be used for walls, floors, and roofs and are often made from materials like timber, steel, or concrete. The panels can be insulated (like Structural Insulated Panels, or SIPs) or non-insulated.
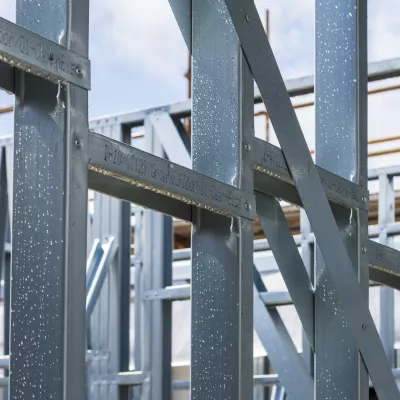
3) Pre-Manufacturing: Structural components
This category combines elements of both volumetric and panelised systems. Hybrid systems offer the flexibility of panelised systems with the speed of volumetric construction, allowing for more complex designs and layouts.
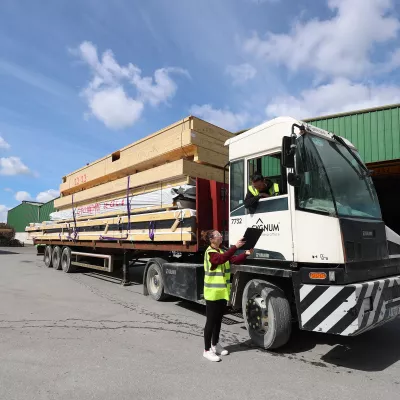
4) Pre-Manufacturing: Additive Manufacturing
Commonly known as 3D printing, this involves the use of digital 3D models to fabricate building components or even entire buildings by layering material. This method offers high levels of customisation and can significantly reduce waste.
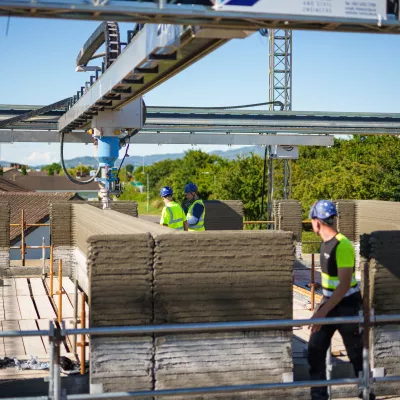
5) Pre-Manufacturing: Non-structural assemblies
This includes non-load-bearing mini-volumetric units (pods) or pre-formed wiring looms. It also includes unitised non-structural walling systems, roofing finishes, and pre-sized materials. This category aims to improve efficiency and safety by pre-fabricating components that are then easily assembled onsite.
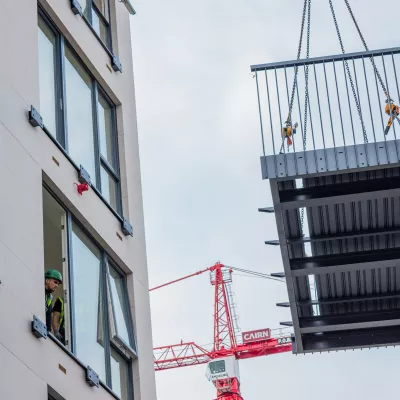
6) Product labour reduction & productivity improvements
This includes traditional building methods but using modern materials and techniques to improve performance. It’s about applying contemporary knowledge and practices to conventional construction approaches.
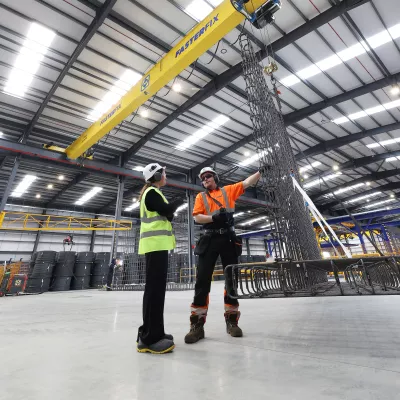
7) Process-led labour reduction & productivity improvements
This category involves innovative techniques applied onsite. These could include novel methods of site preparation, innovative building techniques, or the use of modern, high-performance materials. Examples could include using advanced lifting equipment, robotic construction, or optimised digital workflows to streamline tasks onsite.
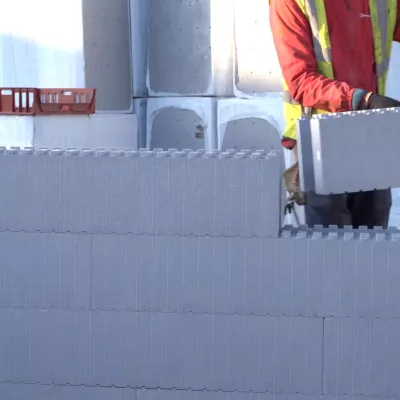