Printed Home Living: Sustainable and Smart
Harcourt Technologies Ltd (HTL) draws from 20+ years of experience in architecture, development, and traditional 3D additive manufacturing. But the latest success of this innovative company is anything but based on how things have always worked in the construction sector.
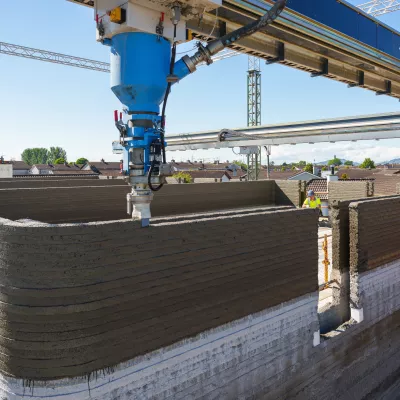
HTL draws from 20+ years of experience in residential construction. But the latest success of this innovative company is anything but based on how things have always worked in the building sector.
Grange Close, an otherwise unassuming street in Dundalk, Co. Louth, has become the first development in the UK or Republic of Ireland with 3D-printed homes. Incredibly, each house is built with layer after layer of printed concrete rather than block by block.
Jandré Oosthuizen, HTL’s Director of Materials & 3DCP Operations, explains that the total build time took just 18 days from start to finish – with a team of only three to four people onsite.
That makes building a house about 30% faster and 50-60% more labour efficient than by using block construction.
Speed is one of the biggest advantages of 3D printing; another major benefit is that it reduces the risk of human error and increases human efficiency.
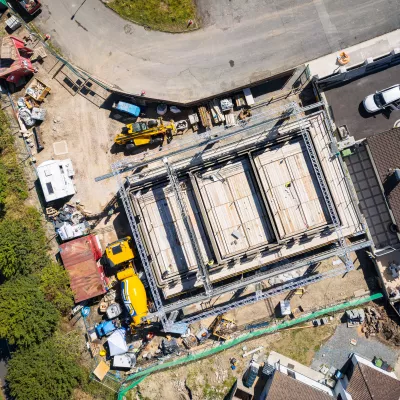
We take the architect’s drawing directly from CAD and execute it onsite using robotic equipment. That means it is highly accurate.
Director of Materials & 3DCP Operations, HTL
Suppliers of additive components, such as window or door manufacturers, can be sent the project specifications and prefabricate items while the build is ongoing.
It eliminates the need for external suppliers to come to site and measure, reducing delays. We just let them know when we need it, and it will fit.
Director of Materials & 3DCP Operations at HTL
This approach, putting a greater emphasis on real-time collaboration between various stakeholders, also makes projects less labour intensive than traditional methods of construction. The HTL team only ever had three to four people onsite at a time, compared to nine or so on a standard build. 3D printing meant there was no need for formwork, further reducing the need for site visits from external providers.
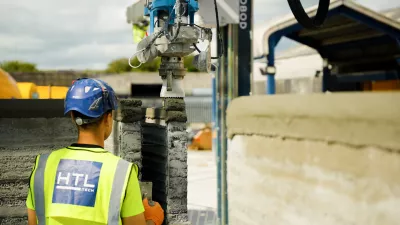
3D printing projects like this open all kinds of possibilities of making construction projects more labour efficient, negating a workforce shortage across the country and meaning more can be done in less time with fewer people. And learning to use a 3D printer doesn’t require expert training either, meaning more people will have access to this technology in a shorter space of time than may otherwise be expected.
If you have been working in traditional construction, any knowledge you have will fit well into this. It’s just about reskilling into a different market. We can train someone up in a couple of months; it’s not as daunting as it sounds.
Director of Materials & 3DCP Operations at HTL